DC Motors
Direct from Round Rock, Texas
TECO-Westinghouse Direct Current (DC) motors are ideally suited to a multitude of industrial and marine applications in which high torque and variable speeds are required. These applications include ship propulsion, mine hoists and steel rolling mills. They also drive many other types of industrial equipment such as fan drives, Banbury mixers and extruders.
To meet the needs of a broad range of applications, our rugged DC motors are available in sizes ranging from 22-inch to 12-foot armature diameters, with available power ratings from 250 hp to over 35,000 hp.
Quality Features / Time-Tested Performance
- High efficiency designs reduce life cycle costs.
- Advanced insulation systems protect against moisture, dust, heat, and contamination.
- Critical area electrostatic coating provides long creepage paths.
- High temperature rise capabilities offer cost economies.
- V-ring, “balanced-spring”, commutator ensures concentricity and prevents distortion.
- High fatigue strength risers increase reliability.
- Lift-away end covers improve accessibility.
- Ruggedly built spiders smoothly transmit torque.
- Integral ventilation package available to continuously circulate cooling air.
- Keyless coupling eliminate inherent disadvantages of key ways.
- Rigid-support, accurately machined bedplates ensure stability.
- Armature wedges and banding assure excellent coil ventilation & accessibility.
- Heavy-duty stators offer outstanding reliability.
- Bearings with self-aligning, spherical seats provide excellent heat transfer.
- Rear mounted cross connections provide accessibility and mechanical stability.
- Full laminated coils reduce eddy current loss.
- Removable shafts available for both continuous and rapid reversing operation.
- Wound-on-pole shunt fields assure excellent heat transfer.
- Sturdy frames provide optimum flux carrying configurations.
- Rear to front ventilation system provides maximum heat dissipation.
More Information
Features:
Cutaway of DC Motor
- Coupling
- Spider
- Armature Laminations
- Armature Cross-Connections
- Main Pole
- Main Field Winding
- Lift-away End Cover
- Frame
- Compensating Winding
- Frame Brush Rigging Arms
- Armature Coils
- Riser
- Brush Holder Brackets
- Brushes
- Commutator Bar
- Commutator Spider
- Shaft
- Bearing
- Spherical Seat
- Oil Rings
- Oil Reservoir
- Pedestal
- Bedplate
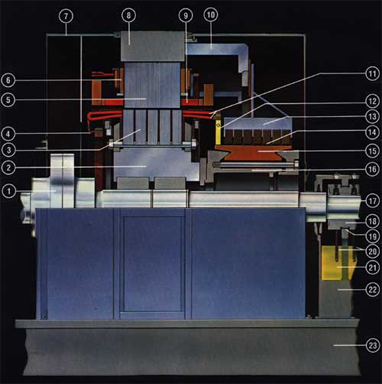
A History of Firsts
Our presence as a world leader in the engineering and production of DC motors is built upon a distinguished record of pioneering achievement in the steel and mining industries.
Working with the steel industry, Westinghouse developed and installed the:
- First electric motors in an American steel mill (1891)
- First electric drive for main rolls
- First reversing mill drive
- First large twin-motor reversing mill drive
Some of our significant achievements in the mining industry include the:
- First application of separately excited shunt-wound DC motors
- First Ward Leonard dragline systems
- First vertical swing motors
- First laminated frame generators
- First dual circuit generator system
Among the many Westinghouse “firsts” in the history of DC motors was the nation’s first reversing rolling mill motor (pictured above), which was installed in 1905.
Perpetuating a proud tradition, TECO-Westinghouse has continued through the years to refine our DC motor product lines with quality enhancing features that secure our position of leadership within the marketplace.
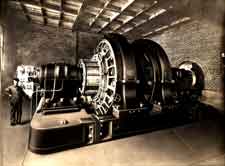